Theodore Lowe, Ap #867-859 Sit Rd, Azusa New York
We are available 24/ 7. Call Now. (888) 456-2790 (121) 255-53333 example@domain.comService details
Give your business a unique logo to stand out from the crowd. We’ll create custom logo for your company.
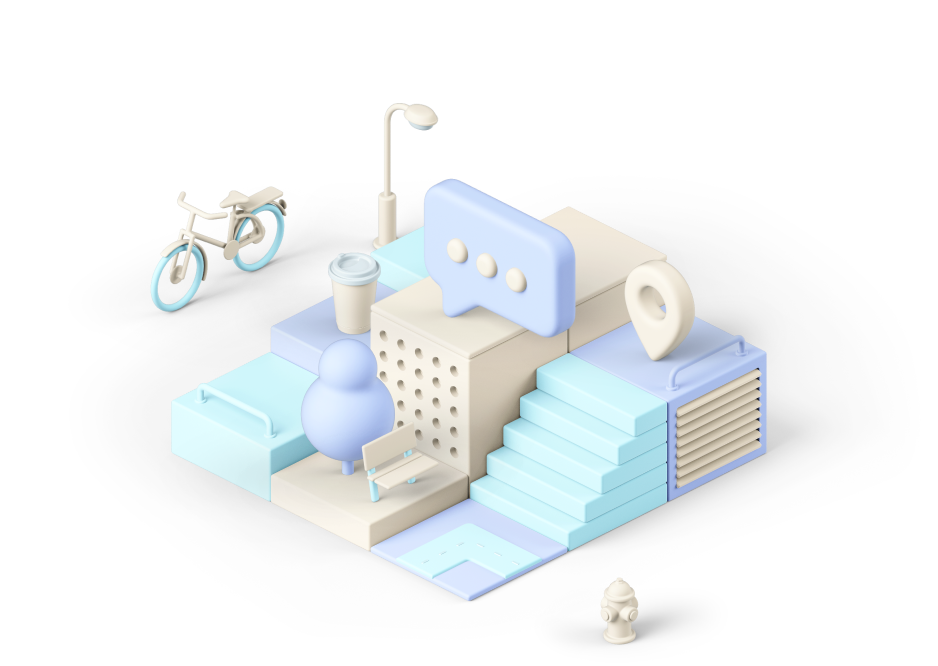
Zinc Flake Coatings
A High-Performance Corrosion Protection Solution
Introduction to Zinc Flake Coatings
Zinc flake coatings are advanced, non-electrolytic coating systems designed to provide superior corrosion protection for metal substrates. These coatings offer an excellent alternative to traditional electroplating methods such as zinc plating and hot-dip galvanizing. Widely used in industries like automotive, aerospace, and construction, zinc flake coatings enhance the durability and longevity of metal components by forming a robust barrier against corrosion.
What Are Zinc Flake Coatings?
Zinc flake coatings consist of fine zinc and aluminum flakes that are dispersed in an organic or inorganic binder. These coatings are applied through a dip-spin, spray, or dip-drain process and are subsequently cured at high temperatures. The result is a dry, thin-layered protective barrier that offers exceptional resistance to environmental factors such as moisture, chemicals, and temperature fluctuations.
Key Benefits of Zinc Flake Coatings
- Superior Corrosion Resistance: Zinc flake coatings provide long-lasting protection against rust and oxidation, withstanding salt spray tests exceeding 1,000 hours. This makes them ideal for harsh environments and extreme weather conditions.
- Thin Coating with High Performance: Unlike traditional galvanizing methods, zinc flake coatings offer a thin-layer application (typically 5-20 microns), ensuring minimal dimensional changes while delivering high-performance corrosion resistance.
- No Hydrogen Embrittlement: One of the major advantages of zinc flake coatings over electroplating is the elimination of hydrogen embrittlement. This makes them particularly suitable for high-strength fasteners and structural components where brittle fractures can be a concern.
- Excellent Chemical and Heat Resistance: Zinc flake coatings exhibit superior resistance to chemicals, oils, and solvents, making them ideal for automotive and industrial applications. They also withstand high temperatures up to 300°C without degradation.
- Environmentally Friendly: These coatings are free from hazardous heavy metals such as cadmium, lead, and chromium (VI), making them compliant with environmental regulations such as RoHS (Restriction of Hazardous Substances) and REACH (Registration, Evaluation, Authorization, and Restriction of Chemicals).
- Enhanced Adhesion and Topcoat Compatibility: Zinc flake coatings serve as an excellent base layer for additional topcoats or sealers, enhancing durability and aesthetic appeal while maintaining friction control properties.
Applications of Zinc Flake Coatings
Automotive Industry
Zinc flake coatings are extensively used in the automotive sector for components such as:
- Bolts, nuts, and washers
- Brake components
- Suspension parts
- Engine fasteners
- Chassis and underbody parts
Aerospace Industry
The aerospace industry benefits from zinc flake coatings due to their lightweight properties and excellent corrosion resistance. Common applications include:
- Aircraft fasteners
- Landing gear components
- Structural joints
Construction and Infrastructure
In construction, zinc flake coatings protect metal structures from rust and environmental damage. They are commonly applied to:
- Structural steel
- Bridge components
- Fencing and guardrails
Renewable Energy Sector
Wind turbines and solar panel structures require corrosion-resistant coatings to withstand harsh outdoor conditions. Zinc flake coatings provide long-term durability for:
- Wind turbine bolts and fasteners
- Solar panel mounting brackets
Application Methods of Zinc Flake Coatings
Dip-Spin Coating
Components are dipped into a coating solution and then spun to remove excess material, ensuring an even application. Commonly used for small to medium-sized parts such as fasteners and springs.
Spray Coating
Ideal for larger or more complex geometries where dip-spin coating is not feasible. Provides controlled thickness and uniform coverage.
Dip-Drain Coating
Components are dipped and then allowed to drain excess coating before curing. Suitable for medium to large parts with uniform surfaces.
Brush or Roller Application
Used for on-site maintenance or repair applications where automated processes are not available.
Zinc Flake Coatings vs. Traditional Coating Methods
Feature | Zinc Flake Coatings | Electroplating |
---|---|---|
Corrosion Resistance | High | Moderate |
Thickness | 5-20 microns | 5-15 microns |
Hydrogen Embrittlement | No | Possible |
Environmental Impact | Low (RoHS/REACH compliant) | May contain hazardous substances |
Heat Resistance | Up to 300°C | Limited |